Table of Content
Many homeowners choose to have metal buildings because of their low maintenance, which is the most significant expense that comes after a homes construction. In addition, materials used in metal buildings are usually coated with a material that protects them from corrosion and rust when exposed to the elements. We encourage you to start your journey with Morton by selecting a model home or cabin from an array of options.
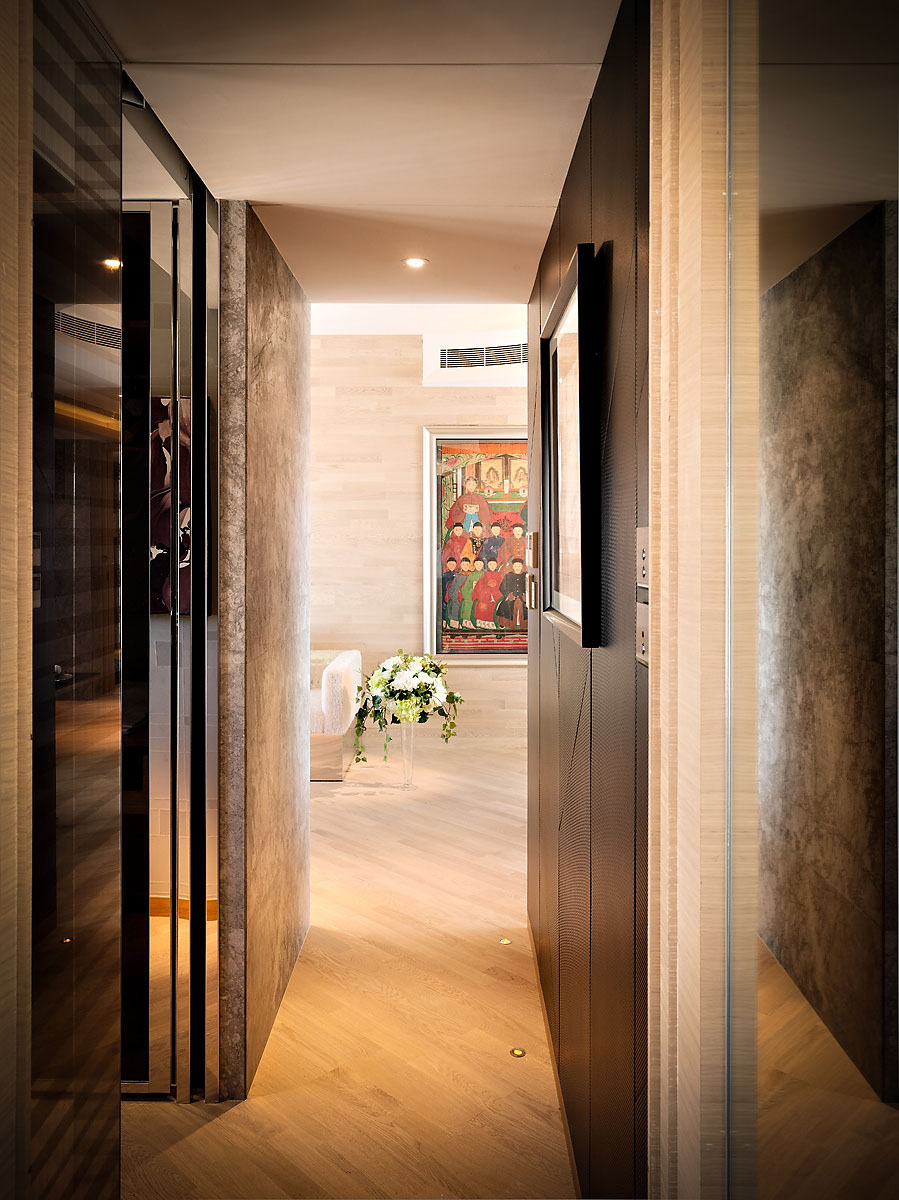
People are always looking for ways to turn their metal carport into a house. The first thing you need to do is get a permit from your local zoning department. This will allow you to make sure that your carport meets all the requirements for a dwelling unit. Once you have your permit, you can start the process of converting your carport into a house. The first thing you need to do is to enclose the carport with walls. Once you have enclosed the carport, you will need to add insulation to the walls and ceiling.
Step 1: Plan the Conduit
Metal buildings can also withstand heavy elements and even disasters such as hurricane, tornado, and sandstorm. Before making a purchase, remember to adjust your needs and budgets to these affordability aspects. Also, make sure you deal with all the permits and licenses before ordering the house to avoid future legal troubles that can cost a lot. Property, such as a house or office building, is a form of long-term investment. As long as you have it, you need to consider the affordability, both for short and long terms.
After labor and material are included, a panel can cost between $40.00 and $60.00. If the building type is noncombustible, a drywall stud must be used with the drywall. Install good vinyl-backed insulation on the walls and roof of your metal building to prevent moisture, warm air, and dry, cold metal panels from interacting. Those who want to be prepared for natural disasters or apocalypses should keep an eye on them because they don’t buckle under pressure. When it comes to designing the floor plan of a steel home, you have complete control over the material choice.
How To Convert A Metal Building Into A Custom Home
Of course, you can paint your building – but you should take steps to do it the right way. After all, a fresh coat of paint is definitely going to help change your metal building into your dream home. Most insulation problems occur because the insulation was not properly sealed from the outside air. This will also prevent unwanted heat transfer, which in turn makes the insulation more efficient.
Be careful not to sand away any undamaged metal, but also be sure to remove as much rust as possible. In either case, be sure to remove as much surface dirt and debris as possible. A clean surface will allow you to paint your shed easily and ensure good adhesion. If you’re doing a bigger job with a three-way switch or multiple circuits, you’ll need more wires. Pull the wire carefully through the conduit and into the LB, then feed it through the wall. It entails the use of a single structural system for all parts of a building.
Rigid Board Insulation
You will need to make sure that your metal building is properly insulated in order to keep the heat in during the winter and the cool air in during the summer. This is especially important if you are planning on using any type of heating or cooling system. This is important for any type of building, but it is especially important for a metal building because of the weight of the metal. You should think about adding finishing touches to a pole barn because it will be used as a living space.
Their passion for craftsmanship and dedication to making your interior and exterior finishes their best are what set them apart from the rest. Those who want to be prepared for natural disasters and pandemics have a better chance of surviving when their belts are free of tension. When it comes to deciding on the floor plan of a steel home, you can make the majority of your decisions from the comfort of your own home.
Home & Cabin Buildings
For a long-term investment, it is a good idea to buy metal homes. Their offset costs are significantly lower than those of conventional homes, and they are significantly less expensive than other types of home construction. The National Association of Home Builders estimates that the average cost of building a metal home is $359,228, which includes all construction, land, and finishing costs. If you already own the land and want to build a smaller building of 40 x 60 square feet, you can expect to pay between $5,000 and $30,000 for the building. Steel or metal buildings are more expensive depending on the location and size of the building.

The increase in demand resulted from the need for more durable housing. Many companies have started offering custom metal building kits for residential homes to meet this growing demand. Metal building manufacturers have sprung up offering a wide array of metal home kits and custom floor plan options to the everyday consumer. Each month we are inspired by the new projects brought to life by these skilled architects and contractors. Footings are not required in metal buildings, but they are important. If your building does not have any footings, it will most likely sag over time.
Furthermore, bricks are more expensive than sheets of metal because bricks are required to cover the entire exterior of a house. Despite the fact that metals will become less expensive over time, bricks are still a more cost-effective option for the vast majority of construction projects. Because these buildings can be designed to meet any residential, commercial, agricultural, or industrial need, you can make any architectural design you want.
That said, spray foam insulation is tricky to install and should be put in by a trained professional. It is also more expensive than other insulation types since it requires special equipment and expertise. Temperature Regulation – The biggest benefit of insulation is its ability to keep your building’s interior temperature stable.
US Department of Defense requires all aviation buildings to be made of metal. You can easily create an ideal floor plan, such as for office, bathroom, storage space, file room, and much more. The lack of internal frames or beams means you can efficiently use all the space.
The National Association of Homebuilders estimated that the average cost of building your own home added up to $359,228. In this guide, you’ll find all you need to know about what goes into the final cost of building a home, and the steps you can take to stay within your budget. Pole barns also work great as garage guest houses, schools, churches, hockey rinks, and retail, office, or warehouse space for businesses. Morton homes and cabins can be designed to meet current lifestyle (i.e., entertaining, storage, hobby) and accommodate future needs (i.e., age-in-place).
Sherman Builders post-frame homes go up much faster than a traditional homes. Steel roofing and siding is also faster to apply than conventional home exteriors. Morton homeowners not only comment on the beauty and flexibility of their homes, but they are also impressed with the efficiency of a Morton metal barn home.
They dont buckle under pressure which may be a deciding factor for those wanting to always be prepared for the impending natural disaster or apocalypse. They can also withstand some pretty extreme weather conditions that would otherwise start to break lumber down. You dont have to worry about splitting, settling, warping or twisting.